|
Typhical
Characteristics |
Property |
Test
Method |
Unit
Typical Value |
Melt
Flow Index (190oC/5.0 kg.) |
ASTM
1238 gm./10 min. |
1.0 |
Density
23oc |
ASTM
D 1505 GM./cm3 |
0.9555 |
Tensile
Strength at Yield |
ASTM
dD 638 kg./cm3 |
22.5 |
Elongation
At Break % |
ASTM
D 638 % |
15 |
Flexuval
Modulus |
ASTM
D 790 kg./cm |
28.200 |
Notched
Izod Impact Strength |
ASTM
D 256 kg./cm |
no
break |
Vicat
Softening Point |
ASTM
D 1525oc |
127 |
|
Note
: Based on injection moulded 3.2 mm thickness type one specimen
of ASTM D 638 |
|
EXTURDER |
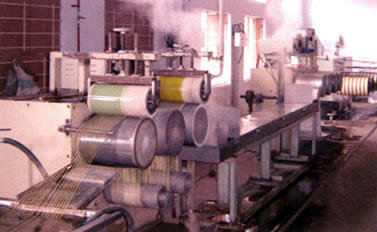 |
The
raw material that is used to produce the filament in this extrusion
process is HDPE granules. Filament can be made in variable colors
and with minimum of 80 dinear to maximum of 300 dinear sizes. |
|
REELING |
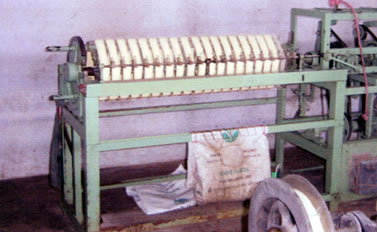 |
The
conversion of the filament to hank form is done in this reeling
process. |
|
WINDING |
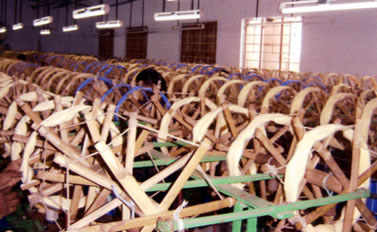 |
The
hank form filament is then winded into small bobbins. |
|
WARPING |
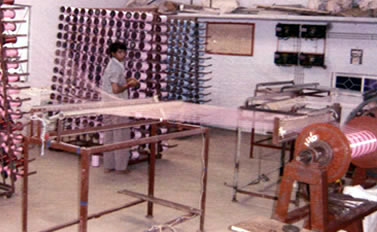 |
Here,
the filament is loaded to the beam for the knitting. |
|
KNITTING |
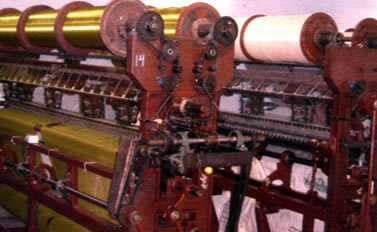 |
The
filament is knitted to fabric form by knitting machines. We
are producing fabric 100 mess/sq. inch to 250 mess/sq.inch.
Knitting is done by quality High-Tech Flat Raschel Machines. |
|
PACKING |
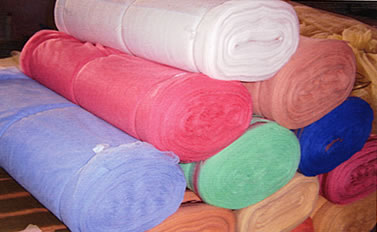 |